PLASTIC LAMINATED PRODUCTS
By Michael Panish
Cabinetry Expert Witness
Download PDF of this article here
This article will discuss plastic laminated products only. Although many other laminated materials are used for residential and commercial applications, plastic laminates are one of the most common products involved in casework claims and personal injuries.
Plastic laminate, often referred to by the manufacturers brand names such as Formica, Wilsonart, Pionite, Laminart, and Nevamar, is one of the most common products in use for both commercial and residential finishes. This type of laminated material is made from layered sheets of paper and resin and is manufactured using high pressure to create a normally durable and water resistant finish. Not only are the various layers of paper laminated during its manufacturing, but the method of attaching the product to a substrate is also known as lamination.
Contact adhesives are normally applied to both the substrate and the plastic laminate and allowed to dry. When the contact cement is dry the two surfaces can be joined by direct contact, and a bond is created. Further topical pressure is applied using rollers or presses to make sure that there is no trapped air or voids between the mated materials. Successful bonding of the mated materials is often dependent upon prior proper preparation of both the substrate and the plastic laminate. Both surfaces must be free of any oil residue or greasy substance that will block the absorption and bond of the contact cement. Both surfaces must be dry and dust free as well. Contact cement must be evenly applied to both surfaces and sufficiently dry prior to mating the two surfaces or a sufficient bond may not be adequately created leading to future failure of adhesion. Contact between both surfaces must be accomplished within a specific period of time, as waiting too long to join the components can lead to possible failure. If contact cement is applied over dirt or oil of any kind a "skinning" can and frequently does occur. While the outward appearance of the dried contact cement may be that both surfaces are ready to be joined, the contaminants may in fact lead to a blocking of the glue products adhesive qualities. This can lead to a release below the mated surface as the contact cement actually attached only to the contaminated areas instead of the intended substrate or laminate product directly.
There are a variety of ways that contact cement can be applied to the component materials. Brushing, spraying and rolling of contact cement is common depending upon the size and complexity of the project. Commercial cabinet shops often roll or spray on the contact adhesive. Depending upon the environment where the laminate is being installed different contact adhesives are required to be used. In an enclosed area, such as an office or hospital environment, water based contact cement is frequently used, if not exclusively required, as fumes from the glue are at a minimum. In respiratory sensitive areas, it is mandatory that certain water based products be used and well ventilated or filtered while drying. Outgassing of glue vapors as the product dries often yields an ammonia like scent that can be irritating to sensitive respiratory conditions. In a cabinet shop environment, where ventilation can be controlled, other more volatile products can be used.
Common problems that have been observed with plastic laminated products include delamination, bubbling, cracking and a complete separation of the plastic laminate surface from the substrate materials. Reasons for the product failures vary depending upon the quality of materials used, the quality of applications, installation practices, chemicals and cleaning products used over long periods of time and stresses created by installers and the environment where the product is installed.
Plastic laminated products are generally not meant for exterior usage. They lack the ultra violet protection in most products and the changes in heat and cold often create differential expansion problems between the substrate and the plastic laminate itself. Some higher quality substrates can be made with water resistant materials; however, the plastic laminate must be properly formed and sealed to achieve a water resistance that is durable.
Forming shapes with plastic laminate is possible, however there are special heaters and presses that are required to properly shape and bend the laminate. Plastic laminate can generally only be formed in one direction. It must be shaped or bent with the "grain" of the laminated paper. The manufacturing process orients the layered papers in one direction to allow for consistent bending.
There are several grades and thicknesses to plastic laminate products. The thinnest materials are referred to as vertical grade plastic laminate. They are meant to be installed on vertical surfaces that will not be exposed to the type of wear and tear that a table top or desk used for storage or writing would encounter. Standard grade laminate is the thickest, and is normally used on horizontal surfaces, but is unable to be bent or curved. In the middle of these two product thicknesses, a special laminate known as "post forming" is the type used for bending plastic laminate around curved surfaces. This type will bend and hold its shape when properly bonded to a curved or rounded substrate material when heat and pressure is used. There are other uses for laminate products including chemical resistant tops. A "chem grade" laminate has a different composition and tends to be more brittle then other laminate products. With all laminates, proper preparation and application is critical for the products durability and ultimate function. The size and radius of a laminated substrate can also be a decisive factor in the longevity of a laminated product. In some applications moisture, ambient changes in temperature and the ability of the substrate to repel these changes can affect the plastic laminated surface by absorption from behind or on the edge of a substrate.
Appropriate installation techniques are also significant in affecting the durability of an installed laminate product. For instance, it is required that a rounded shape be used on cut outs for appliances such as sinks and stove tops. Light fixtures, window kits and specialty vents should have these radius corners as well. If a radius is not made at the corner of a cut, it is probable that the laminate will develop a running line crack emanating from the square corner of that cutout.
Laminate is not generally a good choice for high impact areas or installations where continual dragging or rubbing will occur on the surface. Most plastic laminates are not manufactured with the color all the way through the product. There are specialty products known as "color core" that do have the top color throughout the product. Normally, plastic laminate derives the color and pattern from the top layer of paper during the manufacturing process. Brown craft types of papers constitute the core and base of most laminated products. That base material is often seen in the brown lines found when a piece of laminate is routed and edged regardless of the top surface color of the laminate product.
Fabrication and Installation Problems
- Tearing of the plastic laminate results in jagged and razor sharp edges and can cause serious injuries.
- Delamination can be caused by improper fabrication techniques.
- Laminate failure where defective product manufacturing created a release. Some of the multiple layers from the base layers of paper are not properly bonded to one another and it is discovered after the product is installed and used.
- Stress of the installed product due to improper attachment, inadequate support, or environmental changes and poor design choices.
- Delamination and separation caused by improper maintenance and cleaning techniques.
- Blistering and bubbling caused from exposure to excessive heat generated from sources such as exterior windows that magnify the outside light from the sun.
- Failure of the laminated product due to water and steam in proximity to the laminated products such as in laundry rooms, bathrooms, and kitchen areas.
- Failure of the laminated product due to surface imbalances and moisture absorption.
When is it appropriate to hire a Laminate Expert?
- Serious financial loss has occurred as a result of significant laminate defects or failures.
- Serious physical injuries have resulted from torn or razor sharp laminate edges.
- Defense of a claim made against a cabinetmaker or contractor.
- Tract developer requires expert evaluation to determine the causes of laminate product failures for cabinets, design elements, and casework installed throughout their developments.
- Homeowners waging class action suits against housing developers require expert analysis and investigation into the reasons why their installed products are failing in their homes.
- Contractors and cabinetmakers who have fabricated and installed products also need assistance from an independent expert to help mediate the claims made against them.
Common Lawsuits Involving Laminated Products
- Defective hotel room cabinets, counter tops, and furniture.
- Severe lacerations and life threatening cuts from razor sharp torn laminate.
- Door skins that have pulled off of the doors creating cosmetic and unsafe surfaces.
- Laminated panels that inadvertently release from their intended surfaces, falling from ceilings and walls.
- Buckling, splitting, peeling, and cracking of surfaces creating costly repairs.
- Swollen counter tops from water absorption or chemical damage.
- Delamination of laminate and failed sub surfaces, necessitating complete removal and replacement.
- Architectural products that have failed in the field creating personal injury.
Mike Panish is an expert witness and consultant where one of his areas of expertise is in the field of cabinetry, carpentry, architectural millwork, casework, and furniture. Mike is a cabinet manufacturer and licensed cabinet and millwork contractor in the State of California. He has designed, fabricated, and installed plastic laminated products for over 35 years. Mike's company has fabricated and installed laminated products in government buildings, hotels, hospitals, medical office buildings, labs, courthouses, jails, shopping centers, restaurants, banks, convenience stores, markets, libraries, schools, themed attractions, television, and film production. Mike Panish is highly experienced with most brands of laminates and has personally designed, built, and installed thousands of products used in commercial and residential installations. Mike has been involved in numerous legal cases and retained as the expert, consultant, and testifying witness for plaintiff and defense where defective laminated products have led to serious personal injury and financial loss. Mike has fabricated plastic laminated exemplars for courtroom demonstration. Mike Panish is frequently retained as expert witness for all types of cabinetry related claims for personal injury and product defect cases.
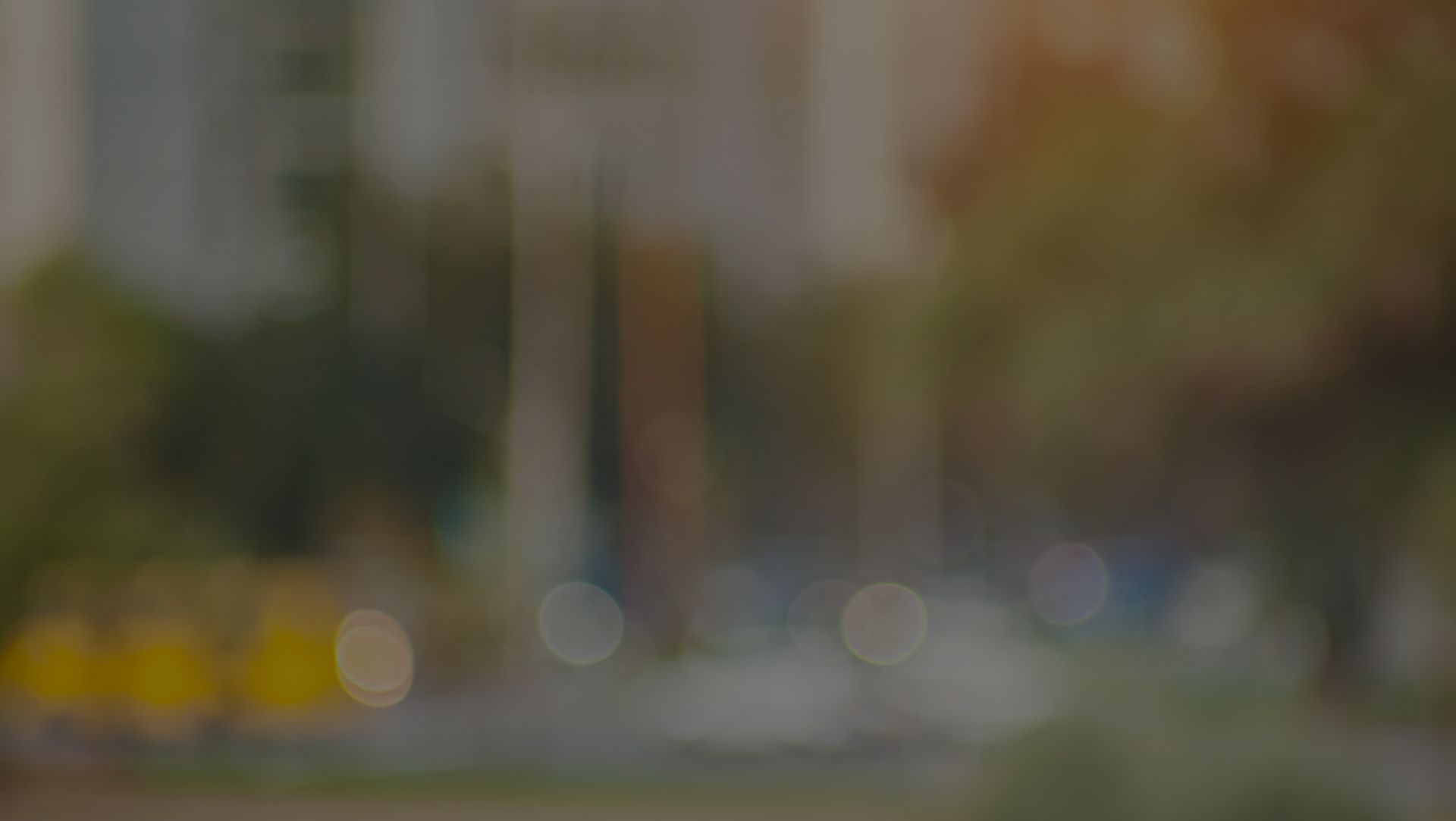